R.W. Fernstrum & Company designs and manufactures keel coolers for commercial vessels. Sean Fernstrum is the current President of the family-owned business operating in the Midwest. The company’s origins come from a need for a small closed-circuit cooling system for Navy landing craft during WWII, which resulted in a prototype of the heat exchangers the company went on to produce later. Its first keel coolers were used by the Navy in the early 1950s.
During the same decade, the company got into commercial work developing cooling systems for commercial fishing vessels, primarily the shrimping fleets in the Gulf of Mexico and South America. Today, commercial work at Fernstrum makes up 90% of its total activities, which explains why the company has great appreciation for the commercial fishing industry. The company’s products are now used for cooling marine propulsion engines, generator sets, reduction gears, and auxiliary systems on board vessels of all sizes worldwide.
“The imagination and ingenuity of the people in the fishing industry is something to be proud of.,” says Fernstrum. “The wide variety of vessels for the different fisheries is something to see, and how they still manage to stay within the regulations. For example, the lobster boats in New England are short and fast, while in the Pacific Northwest or Washington State, some of the vessels are almost as wide as they are long. And then there are also legacy vessels that started out as something else, such as Coast Guard cutters, that get turned into commercial fishing vessels.”
.jpg.medium.800x800.jpg)
Because the staff at Fernstrum are experts at what they do, they can customize their keel coolers to fit these special applications. While the operation of the heat exchanger may be the same, the look of it, and the duty that it is built for can be quite different. They know how to use their heat exchanger’s materials and what can and cannot be done in each environment, which allows for creating the perfect fit for the equipment that is cooled, the vessel and for the region the vessel is operating in.
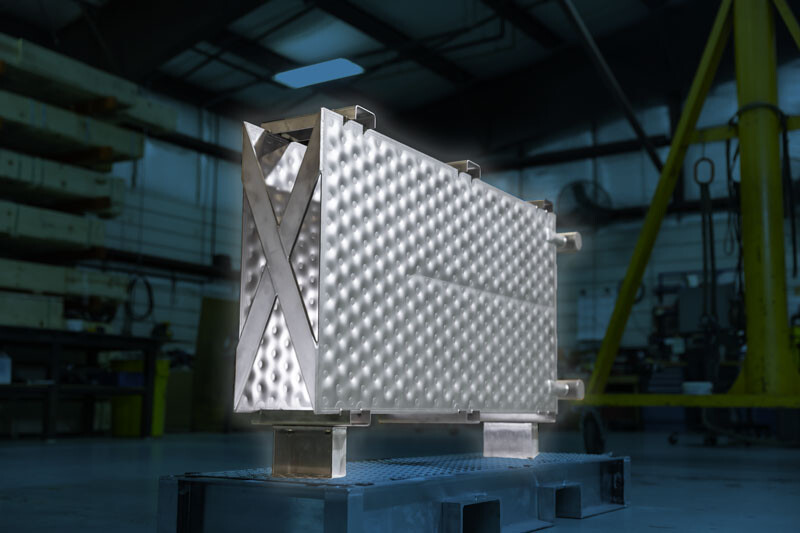
Omega Thermo Products
In 2022, Omega Thermo Products partnered with R.W. Fernstrum & Company to introduce their Laser Plate prime surface heat exchangers to the marine industry. Back then, Fernstrum was looking for a heat exchanger that could be used in bulk cargo, particularly in liquid cargo situations. Apart from that, these are used on some commercial fishing vessels in Europe to work with live wells to maintain water temperatures, explains Fernstrum: “They take this product, attach it to the wall of a live well to help cool that water down, or heat it. We can make it out of a stainless-steel alloy and any number of different exotic metals. By cooling those live wells down, the customer does not have to exchange the water out of those live wells as often, which reduces the cost of the seawater circulation pumps and associated equipment.”
A new product release
Fernstrum just released a new tube size for their heat exchangers. This was the result of the company wanting to bring the size and cost of its heat exchangers down, as their heat exchangers were getting bigger to meet the expanded cooling requirements of higher tier EPA and IMO certified engines. They spent a great deal of time trying to find a tube that was both larger and could maintain the efficiency and structural integrity of the smaller tubes.
The company developed a new tube that can handle 50% more coolant flow, rejects a similar amount of heat as their previous tube, and can hold up to the pressures of the previous larger tube. Finally, by reducing the number of tubes by 30-50% and the overall length, they were able to get into a smaller heat exchanger. This solution is meant primarily for larger engines and should help with the lower-temperature, aftercooler circuits that tend to require much larger heat exchangers than the high-temperature, jacket water circuits. This new tube could have a significant impact on the commercial fishing industry as well, depending on the vessel’s propulsion engines and generators.

A reputation based on innovation
Fernstrum’s reputation is based on innovation, which goes back to the early days. One of the largest innovations took place in the 1970s when new steel alloys came into use for hull materials, which led to problems with heat exchangers in the form of added vibration. Based on customer feedback, the company went back to the drawing board and found a way to absorb the added vibration by using a 56% silver content braze wire. Because silver can expand and contract up to 50% of its size without ever fatiguing, a silver joint is placed where the tubes meet the head, which acts as a shock absorber, like a shock absorber in a car. This is just one example where customer feedback led to changes in Fernstrum’s products. Customer feedback is collected in several ways including through surveys that are sent out at the quote stage and after a customer order has been made.
Fernstrum also works with an extensive network of representatives worldwide, providing customer support when needed and helping to solve minor issues. “We are big believers in developing a good working relationship with our clients. The best way to do that is to have someone local for them to work with, instead of having to call someone on the other side of the planet. That’s why we have local representatives in a lot of different areas globally for customers who require that kind of service”, concludes Fernstrum.